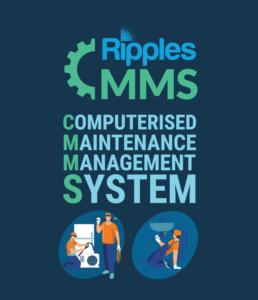
10 Tips to maximize Machine Uptime in factories
Here’s how to maintain your Machine uptime in factories, humming with these key strategies:
Proactive Maintenance is Key
- Implement a proactive maintenance program: Regular checkups for your machines are crucial to catching small problems before they snowball into major breakdowns. This includes routine tasks like lubrication, filter replacements, and wear and tear inspections.
Harness the Power of Machine Monitoring
- Invest in machine monitoring: RTLS devices and other monitoring tools provide real-time insights into your machines’ health. This allows you to identify potential issues early on and take corrective action to prevent downtime.
Empower Your Operators Through Training
- Improve operator training: Well-trained operators are a valuable asset. By ensuring they understand how to operate and maintain the machinery, you equip them to identify and address minor issues, preventing accidental damage.
Keep Spare Parts on Hand to Minimize Downtime
- Spare parts inventory management: Don’t let waiting for replacements stall your production. Maintain a readily available stock of critical spare parts. Analyze your data to identify the parts most prone to failure and prioritize stocking those.
Get to the Root of the Problem
- Root cause analysis: When a machine breaks down, don’t just fix the immediate issue. A CMMS with 5Y’s will help dive deeper to identify the root cause of the failure. This proactive approach helps prevent similar problems from recurring in the future.
Schedule Downtime Strategically
- Schedule downtime strategically: Plan preventive maintenance and repairs during periods of low production to minimize the impact on overall output. This way, you can ensure your machines are serviced without sacrificing productivity.
Empower and Engage Your Operators
- Operator empowerment: Foster a sense of ownership among your machine operators. Encourage them to report any equipment concerns they observe using the panic button, and involve them in the troubleshooting process. This collaborative approach can lead to faster problem-solving.
Motivate Your Teams with Performance Metrics and Incentives
- Performance metrics and incentives: Track machine uptime metrics (MTBR) and establish clear performance goals for both your operators and maintenance teams. Consider implementing incentive programs to reward achieving these goals, fostering a culture of continuous improvement.
Continuous Improvement is a Journey, Not a Destination
- Continuous improvement: Regularly review your machine uptime data to identify areas for improvement. Stay updated on industry best practices and explore new technologies that can further optimize your operations.
Foster a Culture of Maintenance for machine uptime in factories
- Develop a culture of maintenance: Create a company culture that values preventative maintenance and prioritizes equipment uptime. Encourage open communication among abnormality managers about any equipment concerns and ensure they are addressed promptly. By working together, you can create a more efficient and productive factory shop floor environment.
Contact us to learn more about machine breakdown tracking, case study etc
The post Practical tips to maximize Machine Uptime in factories first appeared on RTLS Real-time Location System.