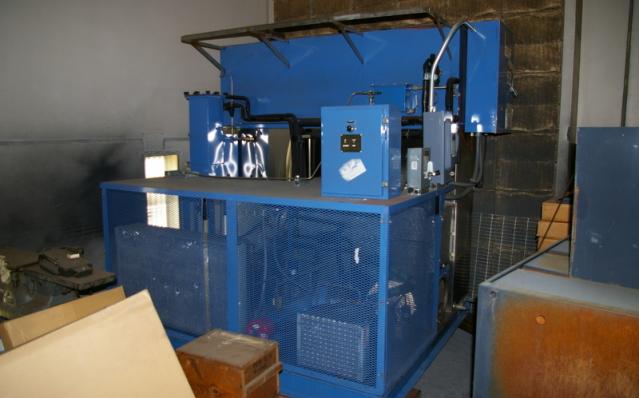
What Exactly Is Vapor Degreasing
Vapor Degreasing represents a cleaning method wherein solvents vaporize and condense onto the targeted object, eliminating the need for water or manual scrubbing. Through this technique, contaminants are effectively removed from parts using solvent vapors. Widely employed in manufacturing, it efficiently cleanses materials like plastic, glass, metal, gold, and ceramic.
Importance of Bearing Lubrication: Maximizing Bearing Lifespan
What Is Electrocleaning: The Ultimate Guide
What Are the Advantages of Using Fluorinated Solvents
How Does Vapor Degreasing Work
In Which Industries Are Vapor Degreasers Used
What Are the Advantages of Vapor Degreasing
Vapor degreasing offers many distinct advantages, including unparalleled cleaning efficacy, consistent results, and independence from operator skill or manual cleaning techniques. By utilizing vaporized solvents, it effectively circumvents issues of cross-contamination inherent in methods reliant on solvent or cleaning solution reuse.
Moreover, using solvents facilitates rapid drying of objects sans the need for secondary drying processes. While the solvents employed in vapor degreasing may carry a higher initial cost than alternative cleaning agents, their continuous recycling within the closed-loop system often renders vapor degreasing a cost-effective cleaning solution over time.
Furthermore, unlike batch or inline systems associated with aqueous cleaners, vapor degreasing eliminates the need for heating water, rinsing, drying parts, or post-cleaning wastewater treatment, streamlining the cleaning process and reducing associated resource consumption.
Vapor Degreaser Solvents Considerations
Best Applications for Vapor Degreaser
When investing in a new or additional vapor degreaser machine, careful consideration of its location is paramount to ensure optimal functionality. Several key factors must be taken into account:
Space Requirements and Clearance
Obtain precise measurements from the manufacturer to ensure that the designated area meets the footprint and accessibility needs of the equipment. Adequate space is necessary for tasks such as solvent loading/unloading, refrigeration repair, and access to control panels and power supplies.
Ceiling Height
Consider the unit’s height, particularly if processing long vertical parts. Ceiling height constraints may necessitate alternative installation methods, such as placing the unit in pits, to mitigate space limitations.
Safety Concerns
To minimise fire hazards, avoid installing the vapor degreaser near open flames, ovens, or areas where arc welding occurs.
Elevation
Depending on the size of the unit, elevation considerations may arise, impacting safety requirements. Larger models may require stairs and rails for safe access.
Process Flow
Ideally, position the unit close to the process area to maintain flow integrity. However, facility layout constraints may limit this option.
Drafts
Prevent cross drafts to minimize vapor removal and product loss. Constructing walls around the unit or placing them in a separate room may be necessary to avoid drafts from air conditioning, doors, windows, fans, or extraction vents.
Ventilation
Ensure proper floor draft to create a laminar flow for vapor removal, as vapors are heavier than air. Avoid drafts in the immediate vicinity of the system to prevent solvent loss.
Humidity Control
Control humidity levels to prevent water vapor absorption, which can lead to hydrolysis in halogenated solvent formulas. Consider enclosing the unit in a humidity-controlled room if necessary.
Pit Concerns
If the unit is located in a pit, ensure proper ventilation and adhere to safety guidelines for air volume and ventilation duration before entering the pit area.
Emergency Preparedness
Plan for emergency scenarios by ensuring clear egress/ingress routes and strategically placing safety equipment such as eye wash stations, safety showers, and fire extinguishers in the vicinity.
Conclusion: Vapor Degreasing
In conclusion, vapor degreasing is a pivotal cleaning method across various industries, offering unparalleled efficiency, consistency, and environmental advantages. Harnessing solvent vapors eliminates the need for water, manual labour, and secondary drying processes, presenting a cost-effective and sustainable solution. Careful consideration of solvent selection, equipment location, and safety measures is imperative to maximise its benefits while ensuring operational integrity and regulatory compliance. As industries continue to prioritise efficiency and environmental responsibility, vapor degreasing is a cornerstone in precision cleaning methodologies.
The post Vapor Degreasing: A Comprehensive Guide appeared first on ORAPI Asia.