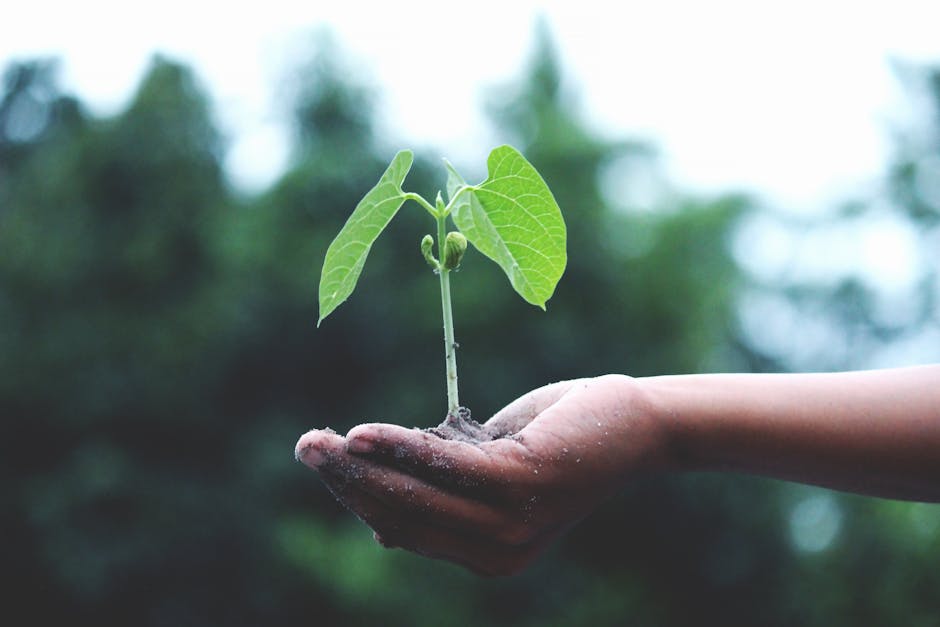
The Art of Smed: Unveiling the Benefits, Pros, and Cons
1. Understanding SMED:
SMED is a methodology developed by Shigeo Shingo in the 1950s to reduce setup times during production processes. Its primary objective is to minimize non-value-added activities and optimize changeover times between different products or setups. By streamlining these processes, companies can achieve higher productivity, reduced costs, improved quality, and increased flexibility.
2. Benefits of SMED:
2.1 Increased Productivity: By reducing setup times, SMED allows for more efficient utilization of equipment and resources. This leads to increased production output and shorter lead times.
2.2 Improved Flexibility: With faster changeovers, manufacturers can respond swiftly to changing market demands and customer requirements. This adaptability enhances their competitive advantage in dynamic business environments.
2.3 Enhanced Quality: SMED encourages standardization and error-proofing techniques during setup processes. This reduces the likelihood of errors or defects occurring during production runs.
2.4 Cost Reduction: SMED eliminates waste associated with extended setup times, such as excess inventory, overproduction, and unnecessary labor costs. These savings contribute to improving overall profitability.
3. Pros of SMED implementation:
3.1 Quick Changeovers: One of the significant advantages of SMED is its ability to drastically reduce changeover times from hours to minutes or even seconds. This enables companies to run smaller batch sizes economically while maintaining high levels of efficiency.
3.2 Increased Machine Availability: By minimizing downtime caused by changeovers, SMED maximizes machine uptime, allowing for more production time and increased overall equipment effectiveness (OEE).
3.3 Employee Engagement: Implementing SMED empowers employees by involving them in the improvement process. This involvement fosters a culture of continuous improvement and encourages teamwork.
3.4 Continuous Improvement: SMED serves as a foundation for implementing other lean principles, such as 5S, Kaizen, and Total Productive Maintenance (TPM). It paves the way for ongoing optimization and continuous improvement throughout the organization.
4. Cons of SMED implementation:
4.1 Initial Investment: Implementing SMED may require an initial investment in training, equipment upgrades, or technology to optimize changeover processes. However, the long-term benefits typically outweigh these initial costs.
4.2 Resistance to Change: Organizations with ingrained processes may face resistance from employees during the transition to SMED. Proper change management strategies and effective communication are crucial to overcome this challenge.
4.3 Complexity in Complex Setups: While SMED is highly effective for reducing setup times in simple operations, it may be challenging to implement in complex setups involving multiple tools, machines, or intricate processes.
In conclusion, Single Minute Exchange of Die (SMED) has proven to be a powerful lean manufacturing technique that can significantly enhance productivity, flexibility, and quality within organizations. The benefits of implementing SMED are numerous, including increased productivity, improved flexibility, enhanced quality, and cost reduction. However, organizations must also consider potential challenges such as initial investments and overcoming resistance to change.
At DS Construction, we recognize the importance of staying at the forefront of manufacturing techniques like SMED to ensure our clients receive the highest quality products efficiently and cost-effectively. We hope this blog post has shed light on the world of SMED and its potential benefits for businesses across industries.
Stay tuned for more informative articles on our blog as we continue to explore the latest trends, techniques, and innovations in the construction industry.